*线品*”上海淞江集团:解决橡胶接头的*切疑问,提*橡胶接头的全部案例,☯全*橡胶接头行业.家通过TS压力管道生产许可证的生产厂家。
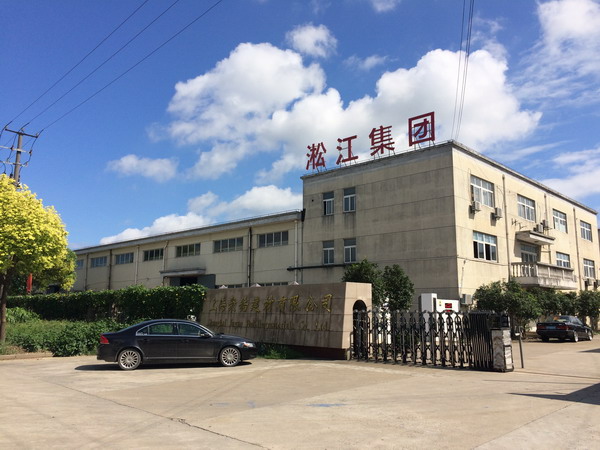
*、胶鞋配方设计的目的和要求
和其他橡胶制品*样,组织胶鞋生产之前,.先 要充分掌握所需原材料的*应条件和价格、工艺装 备的实际情况,然后才能进入配方设计。配方设计 的核心就是选定主体材料和各种助剂,然后再确定
它们之间的配比。所以,配方设计既要满足性能达 标、工艺可行、成本合理等要求,还要取得.*的技 术、经济综合效果。
在设计过程中,要抓住以下几个要点:(1)要重 视整体设计。从总体出发,使各部件之间保持协调 *致,从而获得理想的使用寿命;(2)胶鞋是多部件 制品,为此要协调好各部件胶的硫化速度,因为各部
件厚度各异,受热的时间先后不*,而硫化时间只允 许有*个。这就要求在设计配方时预作考虑,使不 同部件在同*个硫化条件(温度、时间)下同步达到 正硫化;(3)要考虑性能的整体性。因为只有各部件
都达到了各自的性能要求(见表1),才能使全鞋达 到合格要求。
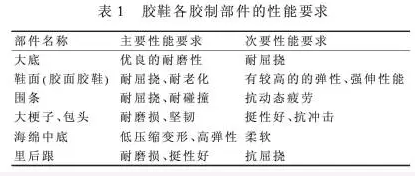
配方设计不仅要满足以上的物理/机械性能的 要求,还要满足加工工艺的要求,主要是三个方面: (1)收缩变形小。将变形量控制在*定范围之内;(2) 良好的粘合性。要求有较高的自粘性、互粘性及较
长的粘性保持期;(3)抗焦烧性。以适应胶料在出型 阶段的返炼次数频繁、受热时间长的.点。因此,要 求各种胶料(.别采用出型工艺的)有较长的门尼焦 烧时间。
二、各部件胶的含胶率
众所周知,含胶率和胶料的性能成比例关系,也 和成本密切相关。过去,在胶鞋方面比较重视高性 能,因此.标准和行业标准所订的物性指标都较 高。为适应这种情况,胶鞋的部件都采用较高的含
胶率,见表2。
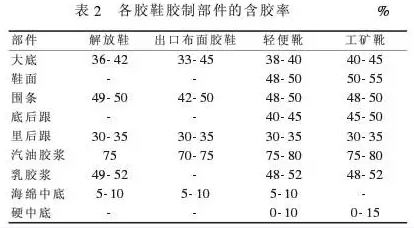
近年来,胶鞋含胶率出现下降的趋势,主要原因 是:(1)人们的消费观念有所转变,旧鞋破损后补了 再穿的情况有所减少,.别在城市消费者中;(2)为 了降低“帮不配底”(帮坏了底远没有坏)的不协调状
况,出现底的剩余功能对橡胶资源是*种浪费。在 这种情况下,适当降低某些部件的含胶率是合理的。
基于以上两种情况,近年来,在胶鞋标准修订中 已对某些指标作了适当的调低,这样做是符合“节能 降耗”精神的。但近年来出现了为追求挖潜创收而 片面降低含胶率的做法,应该予以注意和纠正。
三、各部件胶的设计原则
由于各部件在使用中所起的作用不同,受力条件也各异,因此在设计配方时,应该各有侧重。
1.黑大底
较多采取天然胶和合成胶并用,如NR/SBR/BR 三元共混胶。含胶率应控制在35%~40%,也可掺用 部分胎面再生胶或胎面胶粉。因掺用了合成胶,硫黄用量比全天然胶的硫黄用量有所降低,如1.7~2.0
份;促进剂(如M+D+CZ)的总用量可为1.5~1.8份。 补强剂采取HAF/SRF并用,补强填充剂可用活性陶 土或纳米轻质碳酸钙。以上两项的总量可控制在
50~60份。为了降低成本,也可在性能达标的前提下 另外再添加30~40份普通填充剂。
2.浅色大底
主体材料可使用全天然胶或天然胶与非污染型 合成橡胶(如溶聚丁苯橡胶、顺丁橡胶)的并用胶,但 合成胶的含量以不超过50%为宜,以便于成型操 作。所用各类助剂应为浅色、非污染、强遮盖力的。
用白炭黑补强的话,应添加按其用量8%~10%计算 的二甘醇作为活性剂来抵消硫化延迟效应。另外, 合成胶使用比高的话,还应添加少量增粘剂,以加大 附着力。
3.透明底
生胶可选用溶聚丁苯(如*产SSBR2305)、非 污染型乳聚丁苯(如*产ESBR1502),也可采用天然 橡胶中的白绉片。各类助剂均应选用非污染、不变 色,且折光指数与所用生胶接近的品种。防老剂选
用酚类。硫化活性剂氧化锌由碳酸锌替代。硫黄用 前要过筛。为确保质地透明,补强剂要选用白炭黑, 不得使用遮盖力强的钛白粉、立德粉等。
4.海绵中底
主要功能是缓冲、防震,要求有较高的弹性和* 定的挺性。作为中底,对力学性能的要求不高,故含 胶率控制在5%~10%即够。作为主体材料的天然胶, 选用低号胶即可,甚*还有使用全再生胶的(浅色海
绵除外)。硫黄用量8~9份,促进剂用量12份,之所 以对硫化体系采取这么高的配合量,是为了满足再 生胶(其用量可高达生胶量的好多倍)交联之需,另 外跟微孔胶的表面积大大增加也有关。
5.硬中底(胶面胶鞋专用)
不要求具有海绵中底的柔软性,而要有较高的 硬度。主体材料通常取低标号天然橡胶,及7~8倍 量的再生胶,使含胶率保持在5%~10%的水平,另添 加大量重质碳酸钙、陶土等廉价填料。
6.鞋面(胶面鞋专用)
其是典型的薄型部件,在使用中又要承受频繁、 重复的弯曲变形,需要有较高的含胶率。生胶需选 用高号烟片胶或1号标胶。合成胶的使用比应有* 定上限,以避免出型后收缩太大及压延出型时起绉。促进剂常用组合为M+D+DM或M+D+CZ,由于DM
和CZ都属于后效性促进剂,有较长的焦烧时间,适 合于鞋面胶的多次返炼。炭黑要选用半补强、快压出 等品种,而填充剂则宜选用碳酸钙、陶土等品种。软 化剂则宜选择粘度低、润滑性好的品种,如机油、工
业脂。适量(如5份)的黑油膏有助于压延出型,提高 出型物的光滑度。彩色鞋面胶的设计原则基本同黑 鞋面胶,但补强剂改用白炭黑,防老剂用非污染性的 酚类,也可并用少量高苯乙烯树脂,以提高鞋面的挺
性。
7.底后跟(胶面胶鞋)
基本设计原则与大底相同,主要不同之处在于: (1)含胶率略高,以适应后跟部位与地面的摩擦强度 高于其他部位的.点;(2)后跟的厚度大,传热过程 长,为使各部件.*的硫化程度达到*致,后跟硫速
应适当快于大底的硫速;(3)与大底相比,软化剂用 量应适当减少,以达到提高硬度及减少出型后变形 的双重目的。
8.里后跟
本部件起支撑后跟部位鞋帮的作用,因为*旦 它先被磨损,必然加快后帮挫烂。在配方中添加胎面 再生胶、提高硫黄用量都是有效的针对性措施,参见 配方示例:天然橡胶85,丁苯橡胶15,胎面再生胶
10,硫黄4.4,促进剂M 1.3,促进剂DM 0.6,促进剂 D 0.95,氧化锌4,硬脂酸2,高耐磨炭黑45,轻质碳 酸钙54,陶土60,工业脂2.5,机油15,水杨酸0.25
(防焦剂)。
9.汽油胶浆
设计原则是:(1)含胶率应保持75%~80%的高 水平,因为粘力源自橡胶分子间的交联;(2)胶种应 选择自补强型橡胶,如NR、CR(前者广泛用于传统 胶鞋,后者则用于橡塑鞋);(3)硫化体系用量*般为
3~5份。通常按主体材料(天然胶)的习惯用法,即噻 唑类与呱类并用(促进剂M+D),硫化活性剂氧化锌 的量要多于常规量,而硬脂酸用量要尽可能低(因为 其不利于粘合)。
10.乳胶浆
以天然胶乳为主体,加入各种乳胶专用助剂。乳胶围条浆配方见表3。
四、配色设计
胶鞋的配色设计关系到视感和美学价值的运用。这要由设计人根据自己的见解结合社会大众当 时的审美观、时尚观综合而得。难度在于两个方面:
(1)橡胶的透明性差,因此给配色带来困难;
(2)橡胶 在硫化中经受的高温往往导致着色剂变色,给配色 带来了困难。有些配合剂还会造成污染,使本来配 好的色泽变样。
(1)橡胶的透明性差,因此给配色带来困难;
(2)橡胶 在硫化中经受的高温往往导致着色剂变色,给配色 带来了困难。有些配合剂还会造成污染,使本来配 好的色泽变样。
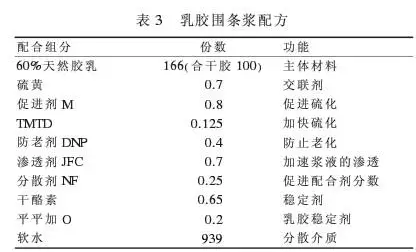
五、橡塑并用配方的设计要点
随着橡塑鞋的出现,橡塑并用在胶鞋中的应用 面迅速扩大。总的来说,设计此类配方要兼顾橡、塑 两相。除了两相都要用的组分(如增塑剂、填充剂、 防老剂)外,凡是专用于*相的,都得单.计量,所
以,经常会遇到以下三方面问题。只要这些问题得 到解决,其他的细节都可按照常规办理,迎刃而解。
1.并用比。传统热硫化胶鞋的主体材料无例外 是橡胶,所以都按橡胶配方设计行事。而橡塑鞋中 不论以哪个相为主,两项都要兼顾。
2.体系中橡胶部分照例要设置硫化体系,.别是 当橡胶相超过20%时更*或缺;而塑料部分则要 设置稳定体系。当然,计算比例也不是完全呆板的, 要视具体情况而定。例如在EVA/PE/NR(50/30/20)的
三元体系中,当考虑硫黄用量时,并非按20%而是按 10%计量。因为在本并用体中,NR处于从属地位。
3.稳定剂。在以树脂为主的并用体系中,稳定剂 *或缺。因为并用后肯定采用塑料的高温加工方 式进行操作,这种高温(*般高于150℃)有可能导致 主体材料降解,所以稳定剂非加*。常用品种为硬
脂酸盐类,如硬脂酸镉、硬脂酸锌或硬脂酸钡等。
六、.种胶鞋及其部件的配方设计
随着胶鞋使用面的日益拓展及出口市场的扩 大,上面介绍的传统设计内容,往往满足不了实际需 要。这种情况常在设计.种胶鞋或新品种时遇到。
1.高透明底
也称全透明底,不同于*般的半透明底。近年来 在出口业务中遇到过这种要求,主要在原材料选用 上比半透明底更严。(1)胶种选择。采用透明度高的 胶种,如顺丁胶、三元乙丙胶和异戊胶,以后者为.
理想,但需进口。(2)助剂选择。各种助剂的折光指数 应该尽可能接近所用生胶的折光指数,见表4。(3)设 计要点。①硫化剂不能用硫黄(因其遮盖力大),要用 过氧化物,如DCP;②补强剂.好用气相白炭黑;③
配用硅烷偶联剂,如A-72(即乙烯基三(β-甲氧基- 氧基)硅烷),以促进各组分分散,它的折光指数与橡 胶的折光指数接近,有助于提高透明度。
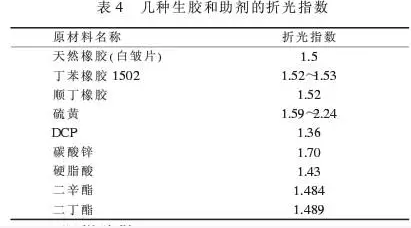
2.阻燃胶鞋
常用于消防、森林防火、矿山的井下作业、冶炼 行业的高温车间等。性能上要求其遇火时有耐燃性, 离火后有自熄性。通常的设计思路是在胶料中加入 阻燃剂,使氧指数降到20~30的范围,即可达到*
般的阻燃要求,能降到20以下则更*。常用的阻燃 剂分无机、有机两大类。阻燃剂*般具有降温、阻隔 氧气的作用,它们是分子结构中含氢氧根(如氢氧化 铝)或卤素的化合物(如氯化石蜡)。在主体材料方
面,以含卤胶种(如氯丁橡胶)或它们与天然橡胶的 并用胶为主,再添加*定数量的阻燃剂及其他配合 剂。阻燃胶鞋既有布面结构的,也有胶面结构的,其 胶制部件都应该按耐燃要求配制。典型配方示例:天
然橡胶70,氯丁橡胶30,硫黄2.1,促进剂2.8,氧化 锌7(包括作为氯丁胶的交联剂和天然胶的硫化活 性剂),硬脂酸3.0,陶土32,炭黑55,液体氯化石蜡
(阻燃剂)13,古马龙8,凡士林2,氧化镁3,固体氯 化石蜡(阻燃剂)30,硼酸锌(阻燃剂)10。
3.抗静电胶鞋
其是*种工作鞋。用于要求导除静电积累的场合 (如生产电子器件的车间),以防止鞋与地面之间因摩 擦产生静电;或者因为静电而影响电子产品的性能。如半导体元件生产车间或电视机组装车间都需使用。
有的医疗器材或药品生产车间也要求工作人员上岗 时穿着抗静电胶鞋,以保证车间符合“无尘”要求。为 此在配方设计时要做到:(1)主体材料要选用体积电 阻相对较大的胶种,如氯丁胶、丁腈胶(体积电阻在
1010~1011Ωcm),但也可以以非.性橡胶为主体材 料;(2)添加.种抗静电剂,如离子型表面活性剂SN 或SP,用量3~5份。配方示例(浅色抗静电大底):天
然橡胶100,硫黄1.4,促进剂1.5,氧化锌5,硬脂酸 2,陶土50,轻质碳酸钙25,抗静电剂SN 5。
4.耐油胶鞋
其是*工作中接触油类人员穿着的工作鞋。主 体材料*般取CR、NBR等耐油胶种。但对耐油要求 不高的,也可掺用非部分.性橡胶,如天然胶、顺丁 胶。硫化体系常采用噻唑类+秋兰姆,如M+DM+
TMTD。增塑剂多采用二丁酯、二辛酯,用量20~25 份。防老剂1~2份,品种不拘。配方示例(浅色耐油大 底):氯丁橡胶80,天然橡胶10,顺丁橡胶10,促进剂
DM 0.5,氧化锌4,氧化镁4,硬脂酸2,促进剂NA- 22 0.5,炭黑40,碳酸钙40,二丁酯15,防老剂D 2。
5.电工*缘鞋
配方设计时需注意两方面的问题:(1)金属氧 化物尽量少用;(2)*般不使用炭黑,因为炭黑的链 状二次结构对电*缘不利,因此较多以陶土来取代。配方示例(*缘胶鞋大底):天然橡胶100,硫黄
0.8,促进剂M 0.5,促进剂DM 1,促进剂TMTD 0.8,氧化锌5,硬脂酸1.5,防老剂D 1.5,陶土 122,工业脂8,凡士林2,石蜡1。
6.耐酸碱胶鞋
用于防止酸、碱接触人体而造成损害,与*般 胶鞋配方大致相同,配方设计时需要注意:(1)耐酸 碱专用助剂硫酸钡*或缺,也可掺用陶土,这两 种填料都能起到防酸碱作用;(2)产品如果是胶面
胶鞋,表面勿涂亮油,而在料中配加石蜡来补偿; (3)促进剂可多用D,实践证明,该促进剂能提高耐 酸碱效果。
配方示例:天然橡胶100,硫黄2.3,促进剂M 1.3,促进剂D 0.35,促进剂DM 0.9,氧化锌5,炉法 炭黑40,防老剂D 1,硫酸钡72,陶土20,固体古
马龙3,液体古马龙13,工业脂9,水杨酸0.2。
7.EVA微孔内底
其是典型的鞋用橡塑并用部件。主体材料由弹 性体(天然橡胶、顺丁橡胶)和EVA、聚乙烯树脂共 同组成。交联剂考虑DCP(因为对橡胶和树脂都能起 交联作用)。发泡体系优先考虑偶氮类的AC,以及助
发泡剂如尿素。配方示例:天然橡胶10,EVA 90,硬 脂酸1.5,氧化锌5,碳酸钙26,发泡剂AC 3.5,尿 素3,DCP 10,钛白粉10。