编辑:淞江集团董帝豪(图片为随机配图,以人士为准)
导读:文章*为介绍橡胶行业有关知识,二为网络优化文章关键词。
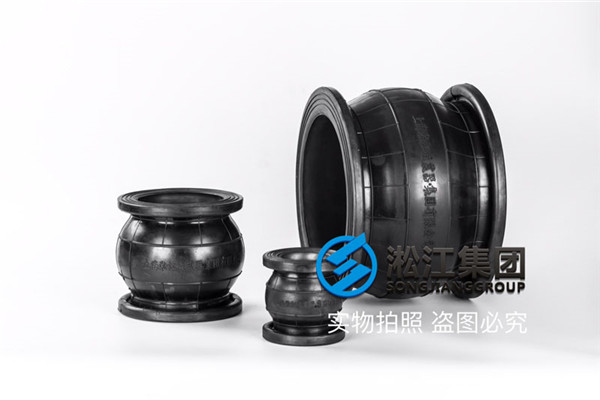
*. 塑炼
塑炼定义:橡胶在外界因素的作用下由弹性物质变为具有可塑性物质的现象叫塑炼。
1. 塑炼的目的
1) 使生胶获得*定的可塑性,适合于混炼等后段工序。
2) 使生胶的可塑性均匀化,使胶料的质量均匀。
2. 需要塑炼胶料的判定:门尼在60以上(理论)门尼在90以上(实际)
3. 塑炼的机器:
1) 开炼机
.点:劳动强度大、生产效率低、操作条件差,但是它比较机动灵活、投资小、适用于变化较多的场合。开炼机的两个滚筒的速比:前比后(1:1.15-1.27)
操作方法:薄通塑炼法、包辊塑炼、爬架子法、化学塑解剂法。
操作时间:塑炼的时间不超过20min,停放时间:4-8小时。
2) 密炼机
.点:生产效率高、操作方便、劳动强度低、可塑度比较均匀,但是高温会使胶料的物理机械性能有所下降。
操作方法:称量→投料→塑炼→排胶→倒合→压片→冷却下片→存放。
操作时间:10-15min停放时间:4-6小时。
4. 常塑炼橡胶
经常需要塑炼的胶料:NR、硬NBR、硬质橡胶。门尼都在90以上的。
二. 混炼
混炼的定义:将各种配合剂加入到橡胶中去制成混合胶。
1. 开炼机混炼
1) 包辊:将生胶包于前辊,用3-5分钟有个短时的预热过程
2) 吃粉过程:把需要加入的助剂按照*定的顺序加入,加入时要注意堆积胶的体积,少了难于混合,多了会打滚不容易混炼。
加料顺序:生胶→活性剂、加工助剂→硫磺→填充、软化剂、分散剂→加工助剂→促进剂
3) 翻炼过程:能更好、更快、更均匀的混炼。
刀法:a、斜刀法(八把刀法) b、三角包法 c、打扭操作法 d、捣胶法(走刀法)
4) 开炼机的装胶容量计算公式:V=0.0065*D*L其中V-体积 D是辊筒的直径(cm) L是辊筒的长度(cm)
5) 辊筒的温度:50-60度
6) 混炼时间:没有具体的规定,看操作员的熟练程度。
2. 密炼机混炼:
1) *段混炼:*次混炼好,混炼的程序:生胶→小料→补强剂→软化剂→排胶→压片机加硫磺、促进剂→下片→冷却停放。
2) 二段混炼:分两段混炼.*段:生胶→小料→补强剂→软化剂→排胶→压片→冷却.二段:母胶→硫磺、促进剂→压片→冷却。
3. 常见的混炼胶的质量毛病
1) 配合剂结团
主要原因有:生胶塑炼不充分;辊距过打;装胶容量过大;辊温过高;粉状配合剂中含有粗粒子或者结团;
2) 比重过大或者过小或者不均匀
原因:配合剂称量不准,错配,漏配、混炼中错加、漏加。
3) 喷霜
主要是由于某些配合剂用量过大、超过其常温下在橡胶中的溶解度造成的。当白色填充过多时也会有白色物质喷出,这时则称为喷粉。
4) 硬度过高、过低、不均匀
原因硫化剂、促进剂、软化剂、补强剂、生胶等称量不准,错加、漏加、造成的,混炼不均造成硬度不均。
5) 焦烧:胶料的早期硫化现象。
原因:助剂配合不当;炼胶操作不当;冷却停放不当;气候影响等。
三、硫化
1. 缺料
1) 模具与橡胶之间的空气无法排出
2) 称重不够
3) 压力不足
4) 胶料流动性太差
5) 模温过高,胶料焦烧
6) 胶料早期焦烧(.料)
7) 料不够厚,流动不充分
2. 气泡、发孔
1) 硫化不足
2) 压力不足
3) 模内或胶料中有杂质或油污
4) 硫化模温过高
5) 硫化剂加少了,硫化速度太慢
3. 重皮、开裂
1)硫化速度太快,胶流动不充分
2)模具脏或胶料粘污迹
3)隔离剂或脱模剂太多
4)胶料厚度不够
4. 产品脱模破裂
1)模温过高或者硫时过长
2)硫化剂用量过多
3)脱模方法不对
5. 难加工
1)产品撕裂强度太好,(如高拉力胶).这种难加工表现为毛边撕不下来
2)产品强度太差,表现为毛边很脆,会连产品*起撕破